プラスチックペール缶の製造工程をご紹介します。
(1) トラックヤード
樹脂原料は1tフレコンでトラックにより輸送されてきます。
原料投入口に樹脂を投入し、指定されたサイロに送ります。
(2) サイロ
原料は計4基のサイロに貯蔵します。
(3) 混合機
サイロより輸送された樹脂は、着色剤と一定の割合で混合し、下部タンクに貯蔵します。
(4) 天板成形機
混合された樹脂は、ヒーターで溶かされて金型内に充填されます。
成形機で出来た製品は、取出機によって取り出され、コンベアで搬送されます。
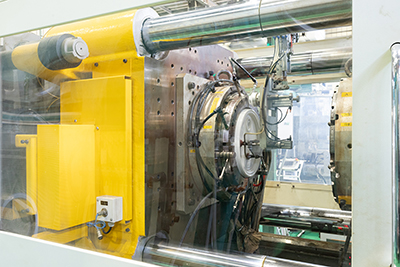
350t 成形機
(5) 缶体成形機
混合された樹脂は、ヒーターで溶かされて金型内に充填されます。
射出成形機で出来た製品は、取出機によって取り出され、コンベアで搬送されます。
24時間全自動で生産します。
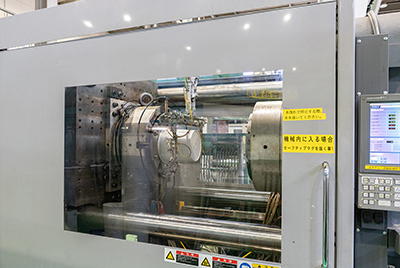
650t 成形機
(6) ライニング
パッキンは2液性のウレタンパッキンで化学反応によって発泡させています。
(7) 天板リークテスター
インサート天板のスパウト部の漏洩検査をします。
(8) キャップ締め
スパウト部のキャップを絞めます。
(9) 天板スタッカー
キャップ締めした天板を積み重ね、パレットに載せ、保管します。
(10) 缶体スタッカー
缶体成形機を出た缶体は、定期品質検査をした後、集約され、10缶ごとに重ねられて2階の倉庫に搬送されます。
(11) 2階倉庫
1階から搬送された缶体を一時保管し、印刷予定に合わせて出庫します。
(12) 缶体印刷機
インクはUVインクを使用し最大4色まで同時に印刷ができます。それぞれの色で使用する版にインクを乗せ、ゴム製のシートに転写させて缶体に印刷します。
(13) ベーリングマシン
缶体に握り(グリップ)をつけます。
(14) 目視検査
缶体内外部の凹み、汚れ、傷などを目視検査で全数チェックします。
こうして千葉工場では業界で唯一のプラスチックペール缶メーカーとして、全自動方式の連続一貫ラインで、24時間稼働で安定供給に努めています。